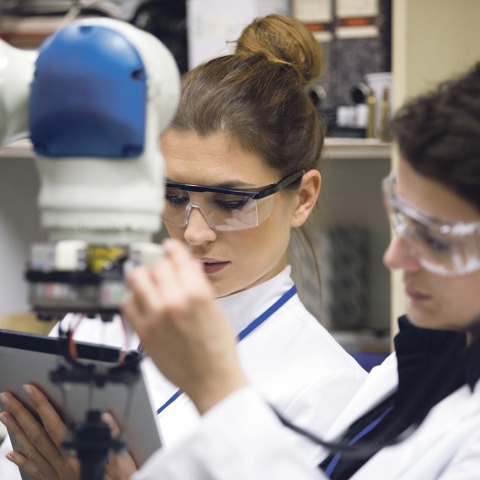
Die vierte industrielle Revolution
Nach den historischen Innovationsschüben mit Dampfmaschine, Fließband und dem Einsatz von Elektronik und Informationstechnologie sind wir mitten in einem Transformationsprozess, der die Unternehmen, die Arbeitswelt und die Gesellschaft grundlegend verändert: „Industrie 4.0“.
Man spricht auch von der „vierten industriellen Revolution“ nach (1.) der Entwicklung mechanischer Produktionsanlagen mithilfe der Dampfkraft im 18. Jahrhundert, (2.) der Einführung arbeitsteiliger Massenproduktion mit Hilfe elektrischer Energie im 19. und Anfang des 20. Jahrhunderts und (3.) der ersten digitalen Revolution durch den Einsatz der neuen Informations- und Kommunikationstechnologien in der zweiten Hälfte des 20. Jahrhunderts.
In den vergangenen Jahren bildeten in erster Linie Informationstechnik und Internet das Fundament für die enormen Produktivitätssteigerungen unserer Ökonomie. Nun sind es digital vernetzte Systeme, mit deren Hilfe eine weitestgehend selbstorganisierte Produktion möglich wird.
Im Kern der Vision Industrie 4.0 steht mit dem „Internet der Dinge“ eine allgegenwärtige Vernetzung von Personen, Dingen und Maschinen. Letztlich ist es die Vernetzung der gesamten Wertschöpfungskette von der Planung über die Konzeption bis zur Produktion und Distribution, die zu einem großen Ganzen werden. Gleichzeitig beschränkt sich die Vernetzung im Zeitalter 4.0 nicht allein auf die Unternehmen und die damit verbundenen Produktions- und Verwaltungsprozesse, sondern wird auf sämtliche innerbetriebswirtschaftliche Vorgänge sowie auf Kunden und Lieferanten, grenz-, länder- und kontinentübergreifend übertragen.
Vernetzte Systeme ermöglichen es, Daten und damit Informationen auszutauschen und somit intelligent miteinander zu verbinden. Dabei steht die Selbststeuerung im Gegensatz zu der bisherigen Zentralsteuerung von Maschinen: Bislang wurden Informationen in unterschiedlichen IT-Systemen gesammelt und von Menschen ausgewertet, die daraufhin Anpassungen vornahmen. Etwa um die Produktionsrate zu erhöhen oder effizienter Güter herzustellen. Dieser Ablauf ändert sich durch Industrie 4.0 grundlegend. In der digitalisierten Zukunft werden alle Maschinen und die von ihnen produzierten Güter mit Sensoren ausgerüstet sein. Sie kommunizieren ständig. Nicht nur untereinander, sondern mit anderen Systemen: Produktion, Vertrieb, Entwicklung, sogar Kunden und Lieferanten werden in die vernetzte Welt eingebunden. Zudem entstehen schließlich neue, oftmals disruptive digitale Geschäftsmodelle, die dem Kunden dank der auf ihn zugeschnittenen Lösungen einen signifikanten Zusatznutzen bieten.
„Mit Disruption meinen wir neue Produkte oder Geschäftsmodelle, die alte oder bestehende ablösen: Neues und Besseres entsteht, Altes wird zerstört. Jede Branche ist von der Digitalisierung betroffen, in vielen sind die Veränderungen grundlegend. Neue Geschäftsmodelle lösen alte ab – in immer kürzeren Zeitabständen“, sagt Kurt Matzler, Professor für Strategisches Management an der Universität Innsbruck.
Das Schlagwort Industrie 4.0 wird mitunter stark politisch verortet. Vielfach wird die Entwicklung nicht revolutionär gesehen, sondern evolutionär als Teil des logischen Fortschritts. Mitunter auch stark verkürzt als nächste Stufe der Automatisierung. Diese verkürzte Sichtweise birgt die Gefahr, eine teilweise doch disruptive Entwicklung zu verschlafen. Dabei kann sich kein Unternehmen der digitalen Transformation völlig entziehen. Unterschiede ergeben sich nur bei der Einschätzung des Tempos der Entwicklung sowie bei der Frage, ob sich die digitale Transformation nur auf die Produktionsseite bezieht oder auch auf die Produkt-/Serviceseite, letztlich mit dem Ziel, Kundenbedürfnisse besser zu erfüllen.
Matzler erkennt drei große Einflussbereiche: Digitalisierung von Produkten und Dienstleistungen, Digitalisierung von Prozessen und Entscheidungen, Digitalisierung von Geschäftsmodellen. Es gelte erstens der Grundsatz, dass alles, was digitalisiert werden kann, digitalisiert wird. Selbst die trivialsten Produkte würden z.B. mit Sensoren ausgestattet, diese Sensoren sammeln Daten und mit diesen Daten werden digitale Services angeboten: Beispielsweise statte Adidas Fußbälle mit Sensoren aus, diese Sensoren sammeln Daten wie Flugbahn, Drall, Schussstärke usw. und über eine App am Smartphone bekommt der User individuelle Trainingstipps. Die nächste Ebene der Digitalisierung stellt die Automatisierung von Prozessen und Entscheidungen dar. Industrie 4.0, Big Data, Algorithmen und künstliche Intelligenz sind hier die Schlagworte. Und die dritte Ebene sind neue digitale Geschäftsmodelle. Hier sind es vor allem Plattformen, die viele Branchen verändern werden.
Für Markus Lassnig, Salzburger Experte für digitale Transformation, hat Industrie 4.0 ein riesiges Anwendungsfeld: „Stark vereinfacht gesagt überall, wo Tätigkeiten bzw. Abläufe in irgendeiner Weise standardisiert sind. Es muss natürlich überall eine Kosten-Nutzen-Abwägung erfolgen, denn nicht jeder rein handwerkliche Prozess ist auch sinnvoll und kostengünstig automatisierbar – doch die Anwendungsmöglichkeiten sind in jedem Fall enorm.“
Auch die Arbeit verändert sich
Diese Entwicklung ist aber nicht auf die Maschinenhalle beschränkt. „Einerseits ersetzt die zunehmende Vernetzung und Automatisierung Arbeitsplätze durch Roboter, künstliche Intelligenzen und neue Maschinen. Auf der anderen Seite steigen die Ansprüche an hoch qualifiziertem Personal sowie ihre Verfügbarkeit auf den Arbeitsmärkten. Neue Jobs entstehen somit durch die Digitalisierung und die neuen Geschäftsmodelle, die sich daraus ergeben. Menschen haben mehr Zeit fürs Wesentliche: Routineaufgaben übernimmt die Maschine, der Mensch kann sich um das Zwischenmenschliche, das Planen, Organisieren und Ausdenken kümmern“, hält Jann Raveling, von der WFB Wirtschaftsförderung Bremen GmbH fest.
Gelebte Kooperationen in Vorarlberg
In Vorarlberg ist 2015 der Wunsch nach Austausch und Vernetzung, auch über die eigene Branche hinaus, entstanden. Gemeinsam mit der Vorarlberger Landesregierung, der Wirtschaftskammer Vorarlberg und der Industriellenvereinigung Vorarlberg initiierte die WISTO ein vorarlbergweites Themennetzwerk. In verschiedenen Formaten sollen sich Firmenvertreter zu ausgewählten Themenfeldern austauschen, Synergien nutzen und Wissenstransfer anregen. Koordiniert werden diese Aktivitäten durch das „V-Netzwerk Intelligente Produktion“. Als offene, kostenlose Plattform für alle interessierten Vorarlberger Unternehmen wird die Auseinandersetzung mit den Themen intelligente Produktion/Industrie 4.0, Weiterbildung und Qualifizierung, (überregionaler) Know-how Austausch, Kooperationen und F&E-Transfer forciert. Dazu werden auf Basis identifizierter regionaler Schwerpunktfelder, Themenworkshops, Vorträge, Firmenbesuche und Studienreisen organisiert, um neue Produktionstechnologien, Trends und Herausforderungen bei Wertschöpfungsprozessen aufzugreifen.
„Wir sind überzeugt, dass wir die digitale Transformation nur zusammen bewerkstelligen können. Diese enge Zusammenarbeit und der intensive Austausch der regionalen Akteure bilden die Basis der Stärke und Effizienz des Wirtschaftsstandortes“, betont WISTO-Geschäftsführer Joachim Heinzl. Weitere Beispiele zeigen die gelebte Kooperation im Bereich Digitalisierung am Standort Vorarlberg: Das Projekt „BodenseeMittelstand 4.0“ unterstützt KMU grenzübergreifend bei der digitalen Transformation. Die Digital Factory der FH Vorarlberg entwickelt mit Unternehmen und akademischen Partnern neue digitale Methoden.
Digitale Lernfabrik
Doch wie finden sich Mitarbeiter oder Lehrlinge in dieser Herausforderung zurecht? Insgesamt sind in Vorarlberg rund 660 Lehrlinge sowie erwachsene Fachkräfte von Industrie 4.0 direkt betroffen. Im WKV-Strategieprozess Dis.Kurs Zukunft wurde deshalb das Projekt Digitale Lernfabrik entwickelt. „Wir als Wirtschaftskammer wollen mit diesem Projekt Menschen in Schlüsseltechnologien qualifizieren, Erfahrungen mit den neuen Technologien sammeln, Lehrende und Ausbilder bei der Vermittlung digitaler Kompetenzen unterstützen und Begeisterung und Interesse für die Technologien der Zukunft wecken“, definiert der WKV-Direktor Christoph Jenny die Ziele der Digitalen Lernfabrik, die am WIFI Campus in Dornbirn angesiedelt sein wird. In der Digitalen Lernfabrik werden zur Vermittlung digitaler Kompetenzen im Rahmen einer praxisorientierten Ausbildung reale Produktionsprozesse nachgebildet: Mit der Anschaffung einer entsprechenden Lerninfrastruktur soll das Konzept Industrie 4.0 im Unterricht für Jugendliche und Erwachsene erleb- und erlernbar gemacht werden.
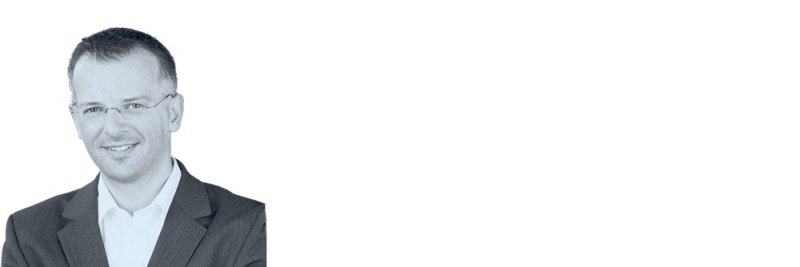
Wissenschaftler
Kurt Matzler
industrie 4.0
Jann Raveling, von der WFB Wirtschaftsförderung Bremen GmbH, hat die heutigen Kernherausforderungen für Unternehmen folgendermaßen zusammengefasst:
- Standardisierung von Schnittstellen: In jedem Unternehmen sind unterschiedlichste Softwares im Einsatz. Die sind selten kompatibel. In der Industrie 4.0 muss aber jedes System mit jedem anderen System kommunizieren können!
- IT-Sicherheit: Viel zu oft berichten Medien von Datenlecks. Nur wenn Daten sicher online verwahrt und ausgetauscht werden können, macht das Internet of Things wirklich Sinn.
- Mensch-Roboter-Kommunikation: Roboter haben gigantisches Potenzial, sind bisher jedoch auf wenige Aufgaben beschränkt. Wenn Menschen und Roboter sicher Seite an Seite arbeiten können, steigt die Verwendung rapide an.
- Individuelle Produktion bis zur Losgröße 1: Individuelle Produktion erfordert auch individuelles Marketing, Vertrieb, Geschäftsprozesse. Das gesamte Unternehmen wandelt sich mit der Industrie 4.0, nicht nur die Maschinen in der Fabrik!
- Selbststeuernde Prozesse in flexiblen Fabriken: Industrie 4.0 heißt nicht zwangsläufig neue Maschinen. Auch viele alte Maschinen lassen sich mit ein wenig Kreativität digitalisieren!
- Big Data und KI – Optimierung der Prozesse durch Datenauswertung: Daten sammeln ist das eine – aber sinnvolle Ergebnisse daraus zu ziehen, das braucht Spezialisten und viel Know-how.
- Arbeit und Ausbildung in der Digitalisierung: Wie werden wir Arbeit künftig organisieren, wenn Roboter und KI Teile davon übernehmen? Was werden wir noch tun? Auch das gilt es, frühzeitig zu bedenken.
- Kundenzentriertes Denken: Der Kunde muss immer im Mittelpunkt jeder Überlegung stehen: Was wünscht er? Wie kann Digitalisierung helfen, das zu erreichen?
Kommentare